6 April 2025
Supply chain management is no walk in the park, right? It's like juggling flaming torches—one wrong move, and everything can come crashing down. When disruptions strike (and they will), they can have a domino effect on your business operations. Whether it's a natural disaster, a supplier going bankrupt, or a container stuck at a port somewhere, these hiccups can derail your entire supply chain. That’s why having a solid plan to tackle these risks is non-negotiable.
In this article, we’ll dive into practical, no-nonsense supply chain risk mitigation strategies so your operations can roll on without a hitch. Let's get into it.
What Is Supply Chain Risk?
Before we dive into solutions, let’s address the elephant in the room—what exactly is supply chain risk? Simply put, it’s any threat that can interrupt the flow of goods and services in your supply chain. Think of it as potholes on a highway. Whether they're big or small, they slow you down and can even bring you to a complete stop.These risks can be internal (system breakdowns, employee errors) or external (disease outbreaks, geopolitical tensions, or even unpredictable weather). Bottom line? If it can throw a wrench in your operations, it qualifies as a supply chain risk.
Why Is Supply Chain Risk Mitigation So Important?
A smooth supply chain is the backbone of your business. Disruptions can lead to production delays, increased costs, unhappy customers, and even reputational damage. On the flip side, mitigating risks not only keeps operations seamless but also gives you a competitive edge. Imagine being the only company delivering on time during a major storm—your customers will remember that.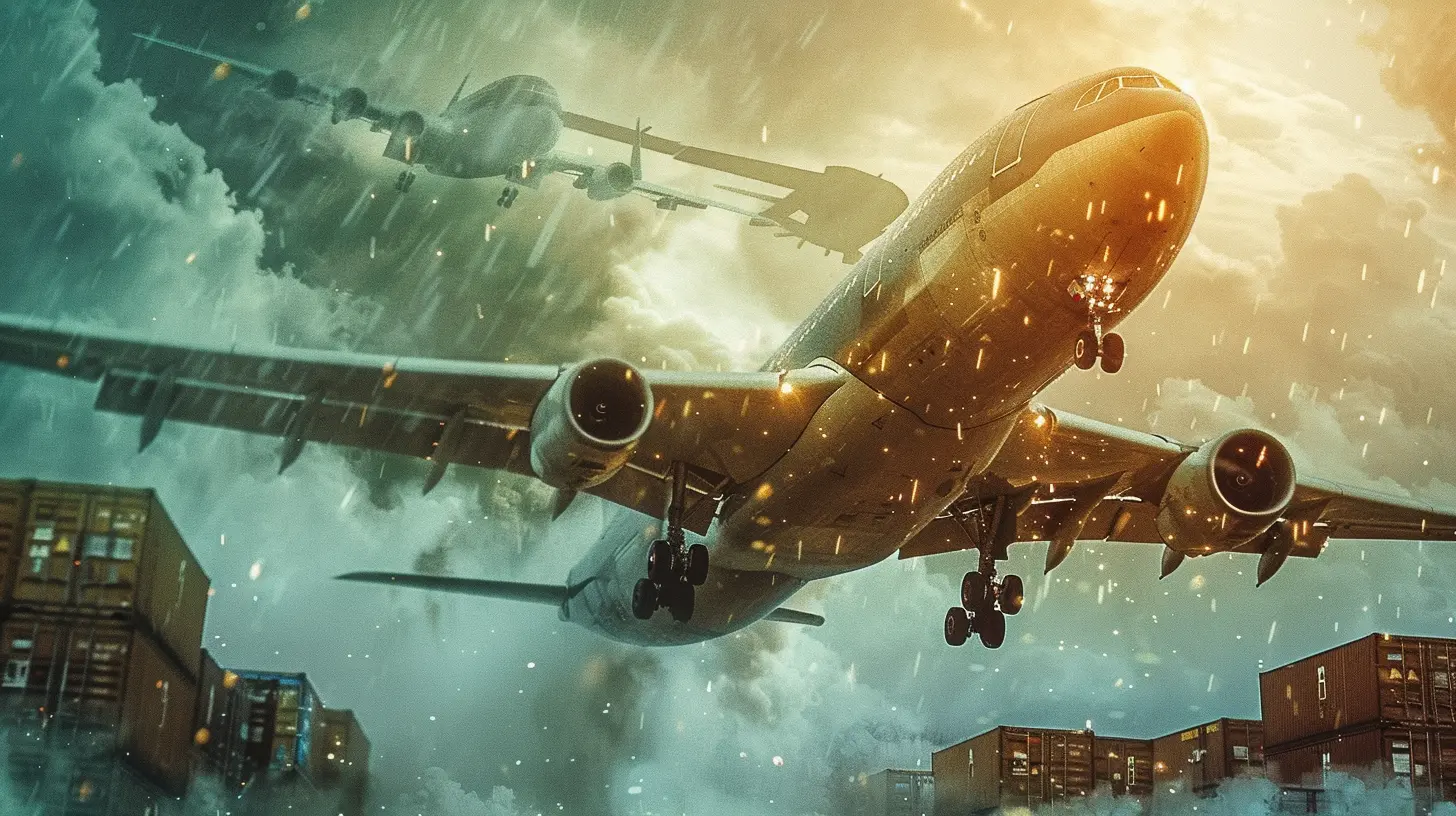
Key Supply Chain Risk Mitigation Strategies
Let’s get practical, shall we? Here are some tried-and-true strategies to mitigate supply chain risks and keep your business running like a well-oiled machine.1. Diversify Your Supplier Base
Relying on a single supplier is like putting all your eggs in one basket. What happens if they can’t deliver? Your entire supply chain grinds to a halt. To avoid this mess, diversify your suppliers.Work with multiple vendors, preferably spread across different regions. This not only reduces dependency but also cushions you from regional disruptions like natural disasters or political unrest.
2. Embrace Technology for Better Visibility
In today’s digital age, playing it by ear isn’t a strategy—it’s a gamble. Use technology like supply chain management software to gain real-time visibility into your operations. This helps you identify bottlenecks early and respond to disruptions proactively.For instance, predictive analytics tools can forecast potential risks (like a supplier delay) before they become full-blown headaches. Think of it as having a crystal ball for your supply chain.
3. Build Strong Relationships With Suppliers
Here’s a golden nugget: Treat your suppliers as partners, not just vendors. A strong relationship means they’re more likely to prioritize you in times of crisis. Communicate regularly, share forecasts, and work on long-term agreements. Trust goes a long way in ensuring continuity.4. Stock Safety Inventory
“Just-in-time” inventory is efficient, but it can leave you in hot water during a disruption. Enter safety stock. Having a buffer inventory of critical materials or products can help you ride out temporary supply chain disruptions.Sure, holding extra inventory comes with carrying costs. But think of it as insurance—you’ll be glad you have it when the unexpected happens.
5. Have a Risk Assessment Framework
Flying blind is a recipe for disaster. Develop a supply chain risk assessment framework to identify vulnerabilities in your operations. Analyze factors like supplier reliability, geographical risks, and economic trends.Once you’ve identified the risks, rank them based on their potential impact and likelihood. This helps you focus on the real troublemakers instead of spreading yourself too thin.
6. Invest in Staff Training
Your supply chain team is your first line of defense. But are they equipped to handle disruptions? Regular training can help them identify risks early and respond effectively.Think of the team as a fire brigade—well-trained staff can put out small fires before they engulf the building.
7. Collaborate With Third-Party Logistics Providers (3PLs)
Sometimes, it’s better to leave it to the experts. 3PL providers specialize in logistics and can keep your supply chain running smoothly, even during disruptions. They have the resources, technology, and expertise to adapt to changes quickly.8. Monitor Your Supply Chain in Real Time
Wouldn’t it be nice to know about a delay before it escalates? Real-time monitoring tools make this a reality. With IoT sensors, GPS tracking, and data analytics, you can stay updated on everything from shipment delays to equipment malfunctions.Think of it as having a dashboard for your entire supply chain—if something’s off, you’ll know immediately.
9. Plan for Emergency Scenarios
Hope for the best, but prepare for the worst. A well-thought-out contingency plan can make all the difference when things go south. Identify worst-case scenarios (like a total supplier shutdown) and outline clear steps to tackle them.Pro tip? Do regular “fire drills” to ensure your team knows the plan inside out.
The Role of Sustainability in Supply Chain Risk Mitigation
Here’s a curveball: Sustainability isn’t just about being eco-friendly—it’s also a risk management strategy. Relying heavily on nonrenewable resources or unethical suppliers can backfire big time. As consumers demand transparency and accountability, aligning your supply chain with sustainable practices can prevent reputational risks and ensure long-term viability.Focus on sourcing responsibly, minimizing waste, and working with suppliers who share your values. It’s not just good PR; it’s good business.
Common Challenges in Supply Chain Risk Mitigation
Let’s be real—putting these strategies into practice isn’t all sunshine and rainbows. Businesses often face challenges like:- Resistance to Change: Implementing new systems or processes can face pushback from employees or suppliers.
- Limited Budgets: Risk mitigation strategies like diversification or advanced tech can be costly.
- Unpredictability: Not all risks (hello, pandemics) can be accounted for in your mitigation strategies.
The trick? Stay flexible and focus on continuous improvement.
Final Thoughts
Supply chain risk mitigation isn’t just a “nice-to-have”—it’s a survival skill in today’s unpredictable business world. Whether it’s diversifying suppliers, leveraging technology, or stocking up on safety inventory, these strategies can keep your operations humming along, no matter what curveballs come your way.Remember, a resilient supply chain isn’t built overnight. It takes planning, investment, and a proactive mindset. But when done right, the payoff is worth it—a smooth, reliable supply chain that keeps your customers happy and your business thriving.
Stephanie McCollum
Implementing proactive supply chain risk mitigation strategies, such as diversifying suppliers and enhancing communication, ensures smoother operations and resilience against unforeseen disruptions. Prioritizing these tactics is essential for long-term success.
April 18, 2025 at 11:20 AM